Manutenção Corretiva em Geradores: Como Garantir o Desempenho Ideal
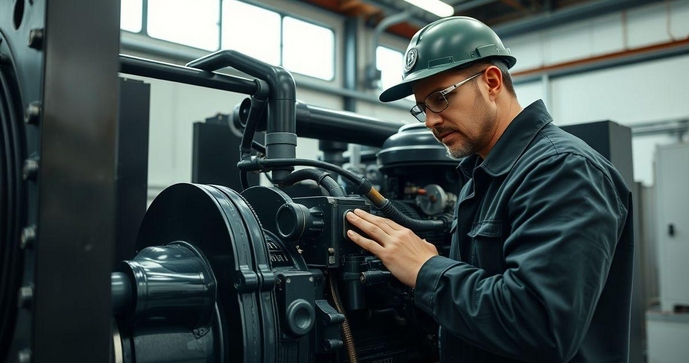
Importância da Manutenção Corretiva em Geradores
A manutenção corretiva em geradores desempenha um papel crucial na operação contínua e confiável de sistemas elétricos. Muitos negócios dependem de geradores para garantir que suas operações não sejam interrompidas por falta de energia, especialmente em setores críticos como saúde, tecnologia da informação e manufatura.
A falta de manutenção regular pode levar a falhas inesperadas, resultando em paradas, o que se traduz em perda de produtividade e receitas. Além disso, a manutenção corretiva ajuda a identificar e corrigir problemas antes que eles se agravem, evitando custos elevados de reparo e substituição. Por meio da realização de manutenções corretivas, é possível aumentar a vida útil do equipamento e promover a eficiência operativa.
Outro ponto importante é que a manutenção corretiva em geradores garante a segurança. Equipamentos em más condições podem representar riscos de segurança para os operadores e para a instalação como um todo, aumentando a possibilidade de acidentes. Portanto, um programa eficaz de manutenção corretiva não só protege o investimento em equipamentos, mas também promove um ambiente de trabalho seguro.
Investir em manutenção corretiva é, portanto, uma decisão estratégica que proporciona benefícios a longo prazo, assegurando que os geradores funcionem de maneira eficiente e segura, minimizando os riscos de falhas e interrupções nos serviços.
Principais Causas de Falhas em Geradores
Compreender as principais causas de falhas em geradores é fundamental para implementar um plano de manutenção corretiva eficaz. Diversos fatores podem contribuir para a deterioração do desempenho dos geradores, e identificá-los rapidamente é crucial para evitar paradas inesperadas.
Uma das causas mais comuns de falhas é a falta de manutenção regular. Sem inspeções e cuidados adequados, componentes essenciais como filtros, fluidos e sistemas de arrefecimento podem deteriorar-se, resultando em falhas operacionais. Além disso, a falta de limpeza pode levar ao acúmulo de sujeira, obstruindo a ventilação e sobrecarregando o motor.
A qualidade do combustível utilizado também pode impactar diretamente o funcionamento dos geradores. Combustíveis contaminados ou de baixa qualidade podem causar danos ao sistema de injeção e ao motor, provocando falhas e uma operação ineficiente. Portanto, é aconselhável realizar testes regulares na qualidade do combustível.
Outras causas de falhas incluem problemas elétricos, como sobrecargas e picos de tensão, que podem danificar os componentes eletrônicos do gerador. Além disso, o desgaste natural dos componentes mecânicos ao longo do tempo é um fator importante, pois peças como rolamentos e alternadores podem falhar se não forem monitoradas e substituídas em intervalos adequados.
Por fim, condições ambientais adversas, como alta umidade, temperaturas extremas e poeira, podem afetar o desempenho dos geradores, resultando em falhas. É fundamental considerar o ambiente em que os geradores estão operando e tomar as medidas necessárias para proteger o equipamento.
Procedimentos para Identificação de Problemas
A identificação de problemas em geradores é uma etapa crítica na manutenção corretiva, pois permite que falhas sejam detectadas precocemente, evitando paradas e custos elevados. Os procedimentos para essa identificação devem ser sistemáticos e abertos a análises detalhadas.
O primeiro passo é realizar uma inspeção visual completa do gerador, verificando sinais de desgaste, corrosão ou danos físicos em componentes visíveis. A presença de vazamentos, fumaça ou ruídos anormais também deve ser notada, pois são sinais de que algo pode estar errado.
Além disso, a análise de dados operacionais é um aspecto crucial na identificação de problemas. É recomendável monitorar e registrar parâmetros como tensão, corrente e frequência durante o funcionamento. Desvios significativos em relação às especificações normais são indicativos de possíveis falhas e devem ser investigados imediatamente.
Outro procedimento eficaz é a realização de testes de diagnóstico. Utilizar equipamentos de medição, como multímetros e analisadores de potência, pode ajudar a identificar falhas elétricas específicas. Testes frequentes nas baterias, sistemas de arrefecimento e no sistema de lubrificação também são recomendados para garantir que todos os componentes estejam funcionando corretamente.
Entrevistar operadores que trabalham diretamente com o gerador pode fornecer informações valiosas sobre o desempenho e as condições do equipamento. Eles podem perceber comportamentos anormais que não são imediatamente evidentes em inspeções visuais ou medições.
Por fim, é aconselhável revisar o histórico de manutenção do gerador. Avaliar os registros de manutenção pode revelar padrões de falhas recorrentes e ajudar a estabelecer uma estratégia preventiva mais eficaz. Com base nessa análise, as equipes de manutenção podem planejar e implementar ações para mitigar as causas raiz dos problemas identificados.
Etapas Essenciais da Manutenção Corretiva
A manutenção corretiva é composta por diversas etapas essenciais que garantem a eficiência e a eficácia do processo de recuperação do gerador. Cada etapa deve ser seguida de forma sistemática para assegurar que todos os problemas sejam resolvidos de maneira adequada.
Primeiramente, a fase de identificação é crucial. Isso envolve a coleta de informações sobre as falhas observadas e a realização de diagnósticos detalhados. As equipes de manutenção devem registrar todos os sintomas e comportamentos anormais que o gerador apresenta, para facilitar a análise posterior.
A próxima etapa é a análise do problema. Aqui, a equipe deve investigar as causas subjacentes das falhas identificadas. Isso pode envolver a revisão do histórico de funcionamento do gerador e a execução de testes específicos para determinar se a falha é elétrica, mecânica ou de outra natureza.
Uma vez diagnosticados os problemas, a etapa de planejamento entra em ação. Essa fase consiste em definir as ações corretivas que devem ser tomadas, incluindo a substituição de peças danificadas, ajustes no sistema ou a realização de limpezas necessárias. É importante estabelecer um cronograma para execução das atividades e garantir que todos os recursos necessários estejam disponíveis.
Após o planejamento, a execução das ações corretivas é a próxima etapa. Isso envolve a implementação das soluções propostas, garantindo que todos os procedimentos de segurança sejam seguidos. A equipe deve trabalhar de forma sistemática, verificando a qualidade das peças usadas e a precisão nos ajustes realizados.
Por fim, a etapa de verificação é essencial. Após a conclusão das correções, o gerador deve ser testado em condições operacionais para assegurar que as falhas foram realmente solucionadas. Monitorar o desempenho do gerador após as correções é vital para confirmar que tudo está funcionando corretamente e que não há outros problemas ocultos.
Essas etapas essenciais formam a base da manutenção corretiva, assegurando que os geradores operem de maneira confiável e eficiente, minimizando os riscos de novas falhas no futuro.
Impacto da Manutenção Corretiva na Durabilidade do Equipamento
A manutenção corretiva é uma abordagem fundamental que impacta diretamente a durabilidade dos geradores. Quando realizada de forma apropriada e em intervalos regulares, essa estratégia não apenas resolve problemas imediatos, mas também contribui para prolongar a vida útil do equipamento.
Uma das maneiras pelas quais a manutenção corretiva melhora a durabilidade é através da detecção precoce de falhas. Ao identificar problemas antes que se tornem críticos, é possível realizar reparos necessários antes que danos irreversíveis ocorram. Isso evita a necessidade de substituições prematuras, economizando custos e aumentando a confiabilidade do gerador ao longo do tempo.
Além disso, o processo de manutenção corretiva frequentemente envolve a limpeza e a lubrificação de componentes mecânicos. Essas práticas ajudam a reduzir o desgaste e a fricção entre as peças em movimento, resultando em um funcionamento mais suave e eficiente. Por conseguinte, componentes que recebem atenção regular tendem a ter ainda mais resistência e durabilidade.
Outro aspecto importante é que a manutenção corretiva pode ajudar a manter o desempenho ideal dos geradores. Enquanto um gerador bem mantido opera em sua capacidade máxima, um gerador com parcimônia na manutenção pode enfrentar problemas de desempenho que causam estresse adicional ao equipamento. Esse estresse pode levar a falhas recorrentes e encurtar a vida útil do gerador.
Por fim, a implementação de uma estratégia de manutenção corretiva também influencia positivamente na percepção de qualidade do serviço prestado. Equipamentos que operam de maneira confiável e que estão em bom estado aumentam a confiança dos operadores e diminui o tempo de inatividade, contribuindo para uma operação geral mais eficiente.
Em resumo, a manutenção corretiva tem um impacto significativo na durabilidade dos geradores, promovendo a detecção precoce de falhas, reduzindo o desgaste e mantendo o desempenho ideal do equipamento. Investir em uma manutenção adequada não é apenas um custo, mas sim um investimento na longevidade e eficiência operacional do seu sistema de geração de energia.
Dicas para Planejar uma Manutenção Corretiva Eficiente
Planejar uma manutenção corretiva eficiente é crucial para assegurar que os geradores funcionem em seu máximo potencial e evitem falhas indesejadas. Aqui estão algumas dicas práticas que podem auxiliar na elaboração de um plano eficaz.
Primeiramente, é essencial realizar um levantamento completo do histórico de manutenção do gerador. Esse histórico fornece informações valiosas sobre as falhas anteriores, os tipos de problemas mais comuns e as soluções implementadas. Com esses dados, é possível identificar padrões e antecipar possíveis falhas futuras.
Em seguida, crie um cronograma de manutenção regular. Embora a manutenção corretiva ocorra em resposta a problemas, ter um cronograma proativo para inspeções pode ajudar a reduzir a frequência e a gravidade das falhas. Estabelecer inspeções trimestrais ou semestrais permite que a equipe identifique problemas potenciais antes que eles se agravem.
Outra dica importante é garantir a melhor capacitação da equipe responsável pela manutenção. Promova treinamentos regulares sobre novos equipamentos, procedimentos e boas práticas. Uma equipe bem treinada é mais eficiente na identificação de problemas e na aplicação de soluções corretivas.
Além disso, mantenha sempre um estoque adequado de peças de reposição. Ter componentes chave disponíveis pode acelerar o processo de reparo, minimizando o tempo de inatividade do gerador. Planeje a reposição de peças com base no histórico de falhas, priorizando aquelas que frequentemente precisam ser substituídas.
A coleta de dados operacionais é outro ponto fundamental. Utilize tecnologias de monitoramento que registrem dados de desempenho do gerador. Essa informação ajuda a identificar sinais de desgaste e indicar quando a manutenção é necessária. A análise contínua de dados proporciona uma visão melhor sobre como o gerador está se comportando sob diferentes condições.
Por fim, envolva todos os stakeholders no processo de planejamento. Isso inclui operadores, engenheiros e gerentes. A comunicação aberta garante que todos tenham uma visão completa das exigências e desafios relacionados ao gerador, permitindo uma abordagem mais colaborativa e eficaz na implementação da manutenção corretiva.
Com essas dicas, você estará melhor preparado para planejar manutenções corretivas que não apenas resolvam problemas imediatos, mas que também contribuam para a eficiência e durabilidade do gerador a longo prazo.
Em resumo, a manutenção corretiva em geradores é uma prática essencial que impacta diretamente a eficiência operacional e a durabilidade dos equipamentos.
Compreender as causas de falhas, aplicar procedimentos adequados para identificação de problemas e seguir etapas estruturadas na manutenção são fundamentais para minimizar custos e maximizar o desempenho dos geradores.
Além disso, planejar de forma eficiente, incluindo o treinamento da equipe e a disponibilidade de peças de reposição, é crucial para garantir que os geradores continuem operando de maneira confiável.
Investir em manutenção corretiva não é apenas um requisito, mas uma estratégia inteligente para assegurar a continuidade e a segurança nas operações que dependem desses sistemas.
Com um bom planejamento e execução, é possível não apenas resolver problemas existentes, mas também evitar recorrências, garantindo assim uma operação mais eficiente e econômica.
Gostou? compartilhe!
Gostou? compartilhe!