Manutenção Preventiva e Corretiva de Grupo Gerador
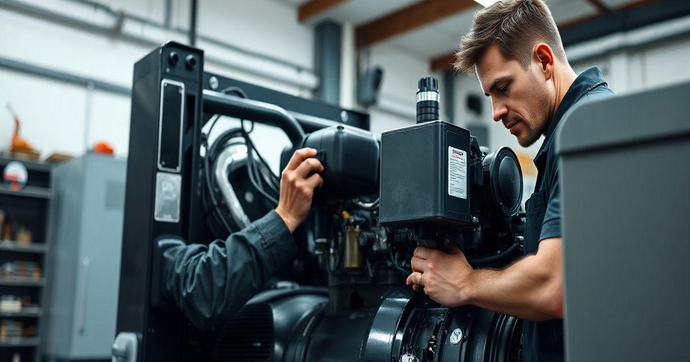
Manutenção preventiva e corretiva de grupo gerador são fundamentais para garantir o funcionamento eficiente e seguro desses equipamentos. Neste artigo, abordaremos a importância dessas práticas, as diferenças entre elas e como realizá-las de forma eficaz. Você aprenderá sobre os principais componentes a serem inspecionados, a frequência ideal para manutenção e os sinais que indicam a necessidade de ações corretivas. Continue lendo e descubra como otimizar a performance do seu grupo gerador.
Importância da Manutenção Preventiva de Grupos Geradores
A manutenção preventiva de grupos geradores é uma prática essencial que visa garantir a eficiência, a segurança e a durabilidade desses equipamentos. Os grupos geradores desempenham um papel crucial em diversas aplicações, fornecendo energia em momentos em que a rede elétrica falha ou em locais onde não há acesso à energia elétrica. Portanto, uma manutenção adequada é necessária para evitar interrupções no fornecimento de energia e garantir a continuidade das operações.
A importância da manutenção preventiva pode ser observada em vários aspectos relacionados à operação e ao desempenho dos grupos geradores.
Redução de Custos
Um dos principais benefícios da manutenção preventiva é a redução de custos operacionais. Quando um grupo gerador é mantido regularmente, os problemas podem ser detectados e resolvidos antes que se tornem falhas graves, que exigiriam reparos custosos e paradas não planejadas. Por exemplo, a troca regular de filtros, a verificação dos níveis de óleo e a inspeção do sistema de refrigeração simplesmente evitam que pequenas falhas se transformem em grandes problemas.
Aumento da Vida Útil do Equipamento
A realização frequente da manutenção preventiva também pode aumentar significativamente a vida útil do grupo gerador. Equipamentos bem cuidados têm um desempenho mais confiável e podem operar por muitos anos sem necessidade de substituição. Quando as partes móveis são lubrificadas corretamente e os componentes são inspecionados, é possível identificar desgastes que, se não tratados, poderiam comprometer o funcionamento do gerador.
Melhoria da Eficiência Energética
Além de evitar problemas futuros, a manutenção preventiva melhora a eficiência energética do grupo gerador. Um gerador bem mantido opera com maior eficácia, consumindo menos combustível para gerar a mesma quantidade de eletricidade. Isso não apenas economiza dinheiro, mas também reduz a emissão de poluentes, contribuindo para um ambiente mais sustentável.
Segurança em Primeiro Lugar
A segurança é outra razão vital para realizar a manutenção preventiva. Grupos geradores que não são mantidos adequadamente podem apresentar riscos sérios, como vazamentos de combustível, falhas mecânicas súbitas ou até incêndios. Por meio de inspeções regulares, é possível detectar problemas de segurança e corrigi-los antes que causem prejuízos. A manutenção preventiva também pode envolver testes de equipamentos de segurança e de proteção, como o quadro de transferência automática para gerador, que asseguram que o sistema opere de forma segura e confiável.
Planejamento Eficiente
Outro aspecto importante da manutenção preventiva é o planejamento. Com um programa de manutenção bem estruturado, as empresas podem programar manutenções em horários que minimizam o impacto nas operações. Isso é essencial em empresas que dependem de fornecimento constante de energia. A manutenção não programada pode resultar em tempos de inatividade que afetam a produtividade e a lucratividade.
Documentação e Registro
A manutenção preventiva também envolve a documentação de todos os procedimentos realizados e a criação de um histórico de manutenção. Esse registro é essencial para acompanhar a performance do grupo gerador ao longo do tempo, além de fornecer informações valiosas para futuras manutenções. Ter um histórico detalhado ajuda os técnicos a diagnosticar o equipamento mais rapidamente e a tomar decisões embasadas sobre as necessidades de manutenção no futuro.
Conclusão
Em resumo, a manutenção preventiva de grupos geradores é uma prática que não deve ser negligenciada. Ela garante não apenas a continuidade do fornecimento de energia, mas também reduz custos, aumenta a vida útil do equipamento e garante a segurança operacional. Investir em um programa de manutenção preventiva sólido é uma decisão inteligente para qualquer empresa que dependa de grupos geradores, pois assegura um funcionamento contínuo e eficiente, maximizando o retorno sobre o investimento.
Diferenças entre Manutenção Preventiva e Corretiva
A manutenção de equipamentos e sistemas é um aspecto crítico para garantir sua eficiência e longevidade. No contexto dos grupos geradores, existem duas abordagens principais para a manutenção: a preventiva e a corretiva. Embora ambas tenham seus objetivos, seus métodos e resultados são bastante distintos. Neste artigo, vamos explorar as diferenças entre manutenção preventiva e corretiva, ajudando a compreender qual é a mais adequada em diferentes situações.
Definições Básicas
A manutenção preventiva é um plano estruturado de cuidados que busca identificar problemas antes que se tornem falhas. Isso envolve ações programadas, como inspeções regulares, limpeza, lubrificação e troca de componentes. O objetivo da manutenção preventiva é evitar interrupções no funcionamento do grupo gerador, prolongando sua vida útil e assegurando um desempenho ideal.
Por outro lado, a manutenção corretiva é realizada após a identificação de uma falha. Ou seja, quando o equipamento apresenta um defeito ou não está funcionando de forma correta, a manutenção corretiva é acionada para resolver o problema. Isso geralmente envolve a substituição de peças danificadas ou a execução de reparos necessários para restaurar a funcionalidade do grupo gerador.
Objetivos e Metas
Os objetivos da manutenção preventiva estão claramente definidos: minimizar o risco de falhas, prolongar a vida útil dos equipamentos e aumentar a confiabilidade. Ao evitar problemas antes que ocorram, a manutenção preventiva assegura que o grupo gerador funcione sempre que necessário, principalmente em situações de emergência.
A manutenção corretiva, por sua vez, busca restaurar a condição operacional do equipamento. Embora seja essencial, pode resultar em custos mais altos devido à urgência das intervenções necessárias. Além disso, há o risco de paradas não programadas, que podem afetar a operação e a eficiência energética.
Custo e Economia
Outro aspecto importante a considerar é o custo associado a cada tipo de manutenção. Enquanto a manutenção preventiva pode exigir um investimento inicial em serviços regulares, os gastos com a manutenção corretiva tendem a ser mais altos a longo prazo. Isso ocorre principalmente porque a manutenção corretiva lida com falhas que podem resultar em danos extensos ao equipamento.
Além disso, com a manutenção corretiva, os custos de reparo e perda de receita durante os períodos de inatividade somam-se rapidamente. Por isso, muitas empresas optam por implementar um programa de manutenção preventiva para evitar esses gastos inesperados.
Programação e Planejamento
A manutenção preventiva é, por natureza, programada. Isso significa que as atividades de manutenção são definidas com antecedência e integradas ao cronograma operacional da empresa. Com um planejamento eficiente, as manutenções podem ser realizadas em horários de baixa demanda, minimizando o impacto nas operações diárias.
Por outro lado, a manutenção corretiva não pode ser planejada, pois depende da ocorrência de falhas não programadas. Isso confere um caráter reativo à manutenção corretiva, que exige que a equipe de manutenção intervenha rapidamente para solucionar o problema e restaurar as operações o mais rápido possível.
Impacto na Operação
As implicações de cada abordagem de manutenção também podem ser sentidas na operação como um todo. A manutenção preventiva, ao garantir que o equipamento esteja sempre em boas condições, ajuda a manter a continuidade das operações e evita surpresas desagradáveis durante o funcionamento. Isso é particularmente importante em setores que dependem de energia constante, onde uma falha pode causar interrupções sérias.
No entanto, quando uma falha ocorre, a manutenção corretiva pode interferir significativamente na produtividade, levando a atrasos e impactos na receita. O tempo de inatividade gerado por uma manutenção corretiva não planejada geralmente resulta em interrupções na operação e pode prejudicar a confiança dos clientes serviços prestados.
Conclusão
Compreender as diferenças entre manutenção preventiva e corretiva é essencial para gerenciar eficientemente os grupos geradores e outros equipamentos. A escolha entre uma abordagem e outra deve ser estratégica e baseada na análise dos riscos, custos e objetivos operacionais. As empresas que conseguem equilibrar ambas as formas de manutenção podem garantir um funcionamento mais eficiente e sustentável de seus sistemas. Para muitas organizações, a integração de práticas de manutenção de cabine primária e preventiva se revela não apenas a mais prática, mas também a mais econômica a longo prazo.
Principais Componentes a Serem Inspecionados
Os grupos geradores são equipamentos complexos que exigem monitoramento e manutenção regulares para garantir seu funcionamento suave e eficaz. A inspeção de componentes é uma parte crucial da manutenção preventiva, ajudando a identificar problemas antes que se tornem falhas significativas. Neste artigo, vamos abordar os principais componentes que devem ser inspecionados regularmente em grupos geradores, garantindo que estejam sempre operando em suas melhores condições.
Motor
O coração do grupo gerador é seu motor, e a inspeção regular desse componente é fundamental. O motor deve ser verificado quanto a vazamentos de óleo, nível de óleo, limpeza do filtro de ar e estado das velas de ignição (nos motores a gasolina) ou injetores (nos motores a diesel). A manutenção geradores a diesel requer atenção especial, pois esses motores podem acumular resíduos que afetam seu desempenho. Um motor bem mantido garantirá uma operação eficiente e minimizará o risco de falhas inesperadas.
Alternador
O alternador é o componente responsável por converter a energia mecânica do motor em energia elétrica. Inspecionar o alternador envolve verificar os terminais de conexão, a condição dos cabos e qualquer sinal de desgaste nos componentes. Flutuações na voltagem ou falhas no fornecimento de energia podem estar diretamente relacionadas a problemas no alternador, portanto, é vital realizar testes regulares de tensão e continuidade para garantir seu funcionamento adequado.
Sistema de Combustível
O sistema de combustível inclui o tanque, as bombas de combustível, os filtros e as linhas de alimentação. É importante inspecionar o tanque para identificar qualquer vazamento ou corrosão, verificar se as bombas estão funcionando corretamente e garantir que os filtros estejam limpos. A contaminação do combustível pode causar sérios danos ao motor, portanto, testes de qualidade e limpeza dos componentes do sistema de combustível são essenciais.
Sistema de Arrefecimento
O sistema de arrefecimento é responsável por manter a temperatura do motor em níveis seguros. Inspecionar o radiador, as mangueiras, a bomba de água e o nível do líquido de arrefecimento é crucial para evitar superaquecimentos, que podem levar a danos catastróficos ao motor. Verifique também se existem vazamentos nas mangueiras e se a ventoinha está operando corretamente. A obstrução do radiador pode comprometer o desempenho do sistema de arrefecimento, portanto, manter esse componente limpo é vital.
Sistema Elétrico
A fiação elétrica e os componentes do sistema elétrico devem ser inspecionados quanto a rastros de desgaste, corrosão e conexões soltas. Verifique a bateria, pois um desempenho inadequado da bateria pode reduzir a eficiência do grupo gerador. Limpe os terminais da bateria e verifique seu nível de carga regularmente. Além disso, é importante testar os fusíveis e relés para garantir que os circuitos estejam funcionando corretamente.
Quadro de Comando
O quadro de comando controla as operações do grupo gerador e é fundamental para seu funcionamento. Inspecione os interruptores, relés e outras conexões no quadro de comando para garantir que não haja sinais de superaquecimento ou falhas. Conexões soltas ou danificadas podem levar a problemas operacionais e interrupções no fornecimento de energia. A manutenção desse componente é necessária para que o grupo gerador opere de maneira confiável e segura.
Silenciador e Sistema de Escape
O silenciador e o sistema de escape desempenham um papel crucial na redução do ruído e na exaustão dos gases do motor. Inspecione o silenciador para garantir que não haja perfurações ou corrosão e verifique se as mangueiras de escape estão em bom estado. Válvulas de escape defeituosas podem causar perda de eficiência e aumento na emissão de poluentes, portanto, a manutenção regular desses componentes é imprescindível.
Filtro de Óleo e Óleo Lubrificante
Finalmente, o filtro de óleo e o óleo lubrificante devem ser examinados regularmente. A troca do óleo e do filtro é uma parte crítica da manutenção preventiva, pois mantém o motor lubricado e em funcionamento suave. O óleo deve ser verificado quanto à cor e textura — óleo sujo ou escuro pode indicar que é hora de uma troca. A má lubrificação pode resultar em desgaste excessivo das peças do motor, podendo levar a falhas sérias.
Ao focar nesses componentes essenciais durante as manutenções programadas, os operadores de grupos geradores podem garantir que seus sistemas permaneçam em ótimas condições de funcionamento, prevenindo falhas imprevistas e mantendo a eficiência operacional. A manutenção regular não é apenas uma questão de boas práticas, mas uma necessidade crítica para assegurar a durabilidade e confiabilidade dos grupos geradores.
Frequência Recomendada para Manutenção
A frequência recomendada para a manutenção de grupos geradores é um fator crucial que determina a eficiência, a segurança e a vida útil do equipamento. A implementação de um cronograma de manutenção adequado não apenas minimiza a probabilidade de falhas, mas também contribui para um funcionamento contínuo e confiável, especialmente em situações de emergência. Neste artigo, discutiremos a importância da frequência na manutenção de grupos geradores e sugeriremos diretrizes para a criação de um calendário eficaz.
Importância da Manutenção Regular
A realização de manutenções regulares é vital para a preservação do desempenho de um grupo gerador. Os geradores são projetados para operar em condições específicas e, sem cuidados frequentes, podem gerar desgastes que comprometem sua funcionalidade. Custos com reparos emergenciais e a interrupção do fornecimento de energia podem ser significativamente reduzidos quando a manutenção é realizada conforme a frequência recomendada.
Diretrizes Gerais de Manutenção
Embora a frequência exata da manutenção possa variar dependendo do tipo de gerador, fabricante e condições de operação, algumas diretrizes gerais podem ser seguidas:
- Manutenção Diária: Inspeções visuais devem ser realizadas diariamente, especialmente em locais onde o gerador é utilizado de forma contínua. Verifique sinais de vazamentos, ruídos anormais e níveis de óleo e combustível.
- Manutenção Semanal: Uma revisão semanal deve incluir a verificação dos níveis de combustível e a limpeza do filtro de ar. Além disso, teste o sistema de arranque para garantir que todos os componentes estejam operacionais.
- Manutenção Mensal: A cada mês, é essencial realizar um teste do sistema sob carga. Isso não apenas garante que o gerador funcione sob condições normais, mas também permite a identificação de potenciais problemas com mais antecipação.
- Manutenção Trimestral: A manutenção trimestral deve incluir a troca do óleo e do filtro de óleo, assim como a verificação do sistema de arrefecimento e do sistema elétrico. A limpeza dos componentes também é recomendada neste intervalo.
- Manutenção Semestral: Inspeções mais aprofundadas devem ser realizadas a cada seis meses, abrangendo a verificação do alternador, do sistema de combustível e da bateria. Este é também o momento ideal para substituir peças com desgaste visível.
- Manutenção Anual: A manutenção anual deve incluir uma revisão completa do sistema, incluindo a análise de todos os componentes e a realização de serviços mais complexos, como teste de resistência de isolamento no sistema elétrico e análise de vibração do motor.
Considerações Adicionais
Além das diretrizes mencionadas, é importante considerar que alguns fatores podem influenciar a frequência das manutenções:
- Condições de Operação: Ambientes mais agressivos, como locais com poeira excessiva ou temperaturas extremamente altas, podem exigir manutenções mais frequentes.
- Tipo de Carga: A natureza da carga que o gerador suporta também pode afetar a frequência das manutenções. Cargas variáveis ou irregulares podem demandar mais atenção do que cargas constantes e estáveis.
- Idade do Equipamento: Grupos geradores maiores e mais antigos podem deteriorar-se mais rapidamente do que novos, exigindo uma frequência de manutenção mais alta para prevenir falhas.
Impacto na Decisão de Compra
Ao considerar a comprar gerador, a frequência de manutenção deve ser um dos fatores analisados. Geradores que requerem manutenções mais frequentes podem acarretar custos operacionais mais altos a longo prazo, enquanto modelos mais novos e bem projetados podem oferecer períodos de manutenção mais longos, contribuindo para uma operação mais econômica.
Benefícios de um Cronograma de Manutenção
Estabelecer um cronograma de manutenção claro e de fácil acesso é uma abordagem inteligente para garantir eficiência no gerenciamento de grupos geradores. Entre os principais benefícios de manter um calendário regular de manutenções, destacam-se:
- Prolongamento da Vida Útil: A manutenção regular ajuda a preservar a integridade dos componentes, estendendo a vida útil do gerador.
- Minimização de Falhas: O monitoramento constante e a atenção a detalhes podem prevenir falhas abruptas, assegurando que o sistema funcione sem interrupções.
- Eficiência Energética: Manutenções realizadas em intervalos adequados garantem que o gerador opere da maneira mais eficiente possível, resultando em menor consumo de combustível.
- Segurança: Manter uma rotina de manutenção regular reduz o risco de falhas catastróficas, melhorando a segurança tanto dos operadores quanto do equipamento.
Em conclusão, a frequência recomendada para a manutenção de grupos geradores é um elemento decisivo para garantir um desempenho ótimo e durabilidade do sistema. Seguir um cronograma adequado, que considera as diretrizes mencionadas e as condições específicas do ambiente de operação, assegura que os geradores operem com confiabilidade e eficiência. Essa abordagem não só evita interrupções indesejadas como também contribui para um ambiente operacional seguro e estável.
Sinais de Que a Manutenção Corretiva é Necessária
A manutenção corretiva é um aspecto crucial da gestão de grupos geradores, garantindo que o equipamento funcione de maneira eficiente e segura. Embora a manutenção preventiva, realizada de forma regular, possa minimizar muitos problemas, às vezes é inevitável que surjam falhas. Para evitar danos mais sérios ao equipamento e garantir sua operação, é fundamental reconhecer os sinais de que a manutenção corretiva é necessária. Neste artigo, serão apresentados os principais indicadores que mostram que é hora de agir e realizar reparos no seu grupo gerador.
Sinais Visuais de Desgaste
Um dos primeiros sinais de que a manutenção corretiva pode ser necessária é a presença de desgastes visíveis nos componentes do gerador. Inspecionar regularmente o motor, alternador, sistemas de combustão e outros componentes essenciais pode revelar vazamentos de óleo, corrosão e rachaduras. Se você notar vazamentos significativos ou sujeira acumulada em áreas críticas, isso pode indicar um problema que precisa ser solucionado imediatamente.
Ruídos Anormais
Os ruídos que o gerador emite durante a operação podem fornecer dicas importantes sobre sua condição. Se você começar a ouvir sons anormais, como batidas, rangidos ou chiados que não estavam presentes anteriormente, é hora de investigar. Esses sons podem ser um sinal de que os componentes internos, como buchas e rolamentos, estão desgastados ou danificados, indicando a necessidade de manutenção corretiva para evitar falhas severas.
Desempenho Inadequado
Um desempenho abaixo do ideal pode ser um forte indicador da necessidade de manutenção corretiva. Se o gerador não está gerando a quantidade esperada de energia ou se está apresentando flutuações de tensão, pode ser necessário investigar a causa desses problemas. Desempenho inadequado pode ser causado por falhas nos sistemas de combustível, como filtros entupidos ou bombas danificadas, exigindo intervenções corretivas.
Temperaturas Elevadas
Sobrecargas e temperaturas excessivas podem indicar um problema potencial que requer manutenção imediata. O sistema de arrefecimento deve ser monitorado para garantir que o motor não superaqueça, pois temperaturas muito altas podem causar danos permanentes. Se o indicador de temperatura estiver consistentemente alto ou se o gerador desativar devido a superaquecimento, pode ser necessário inspecionar o sistema de arrefecimento, incluindo o líquido refrigerante, radiador e mangueiras.
Falhas no Arranque
Dificuldades ao dar partida no gerador são um sinal claro de que a manutenção corretiva é necessária. Isso pode ser causado por uma variedade de problemas, incluindo uma bateria fraca, falhas no sistema elétrico ou problemas com o motor. Se o gerador não liga ou apresenta dificuldades para manter a ignição, deve-se verificar os componentes do sistema elétrico e as conexões, além do estado da bateria e do motor.
Fumaça e Emissões Anormais
A presença de fumaça ou emissões incomuns durante a operação do gerador é um sinal alarmante de problemas internos. Fumaça preta, branca ou azul pode indicar diferentes problemas, como combustão inadequada, vazamentos de óleo ou outros problemas internos. É importante abordar essas questões imediatamente, pois podem levar a danos adicionais e custos elevados se não forem tratados rapidamente.
Indicadores no Painel de Controle
Os painéis de controle modernos dos geradores oferecem uma diversidade de indicadores e alarmes que podem ajudar na identificação de problemas. Fique atento a qualquer luz de aviso ou alarme que indique uma falha de sistema, que geralmente requer manutenção corretiva. Desvios nos parâmetros normais, como variações na pressão do óleo ou avisos de sobrecarga, devem ser investigados imediatamente para evitar complicações maiores.
Histórico de Manutenção
Aproximar-se de um histórico de manutenção regularmente pode ajudar a identificar quando a manutenção corretiva é necessária. Se o gerador já passou por reparos frequentemente ou se algumas partes já foram substituídas, pode ser um sinal de que algo mais sério está acontecendo. Recomenda-se manter registros meticulosos de todas as manutenções realizadas, permitindo que os operadores visualizem facilmente padrões ou repetições de falhas.
Conclusão
Identificar os sinais de que a manutenção corretiva é necessária é essencial para garantir a confiabilidade e a eficiência dos grupos geradores. Momentos de falha ou condições adversas podem ter um custo elevado, tanto em termos financeiros quanto em prejuízos operacionais. Se você perceber qualquer um dos sinais mencionados, não hesite em entrar em contato com profissionais qualificados para uma avaliação detalhada e realizar as correções necessárias. Fazer isso não apenas prolongará a vida útil do gerador, mas também assegurará um desempenho ideal e a segurança das operações que dependem dele.
Benefícios da Manutenção Regular
A manutenção regular de grupos geradores é uma prática essencial que traz múltiplos benefícios, garantindo não apenas a eficiência dos equipamentos, mas também a segurança operacional e a economia a longo prazo. Neste artigo, exploraremos os principais benefícios da manutenção regular, demonstrando como ela pode impactar positivamente o desempenho e a durabilidade dos grupos geradores.
Prolongamento da Vida Útil do Equipamento
Um dos benefícios mais significativos da manutenção regular é o prolongamento da vida útil do grupo gerador. Ao realizar inspeções e trocas de componentes periodicamente, é possível evitar o desgaste excessivo e identificar problemas em seus estágios iniciais. Isso significa que o investimento em um grupo gerador se transforma em economia ao longo do tempo, permitindo que o equipamento funcione de forma eficiente por muitos anos. Manter o gerador em boas condições é, portanto, uma estratégia inteligente para garantir o máximo retorno sobre o investimento.
Redução de Custos com Reparos e Paradas
A manutenção regular permite a detecção precoce de problemas, evitando a necessidade de manutenções corretivas mais complexas e caras. Quando os problemas são identificados a tempo, é possível realizar reparos menores e mais econômicos, que não resultam em paradas inesperadas. As paradas não planejadas acarretam perdas financeiras significativas, tanto pela incapacidade de fornecer energia quanto pelos custos associados ao reparo de falhas maiores. Assim, a realização de manutenções em intervalos regulares desempenha um papel vital na redução de custos operacionais.
Otimização do Desempenho Energético
Geradores bem mantidos operam com eficiência superior, consumindo menos combustível e, consequentemente, reduzindo os custos de operação. Isso não apenas é mais econômico para a empresa, mas também é uma prática mais sustentável, uma vez que resulta em menos emissões de gases poluentes. A eficiência energética proporcionada pela manutenção regular significa que o gerador pode gerar mais eletricidade com a mesma quantidade de combustível, contribuindo para uma operação mais sustentável.
Aumento da Confiabilidade e Disponibilidade
A manutenção regular garante que o grupo gerador esteja sempre disponível e operando de maneira confiável. A possibilidade de falhas inesperadas é significativamente reduzida quando o equipamento é examinado e cuidado em intervalos regulares. Isso é especialmente crucial em setores onde a continuidade do fornecimento de energia é crítica. Ter a certeza de que o gerador funcionará quando necessário proporciona uma tranquilidade significativa para os operadores e para os negócios como um todo.
Segurança do Operador e do Equipamento
A manutenção regular também desempenha um papel crucial na segurança dos operadores e do próprio equipamento. A falha de um gerador pode levar a situações perigosas, como incêndios ou explosões, especialmente se partes do sistema elétrico estiverem comprometidas. Através de inspeções e manutenções preventivas, é possível minimizar esses riscos, garantindo um ambiente de trabalho seguro. A segurança deve sempre ser uma prioridade e, ao manter o gerador em ótimas condições, estamos protegendo tanto os operadores quanto o investimento feito no equipamento.
Documentação e Histórico de Manutenção
Realizar a manutenção regular permite uma melhor documentação e histórico de serviços prestados ao grupo gerador. Ter um registro meticuloso das manutenções realizadas ajuda na avaliação do desempenho do equipamento ao longo do tempo e proporciona um guia valioso para futuras manutenções. Além disso, esse histórico pode ser extremamente útil em situações de garantia ou quando é necessário justificar a responsabilidade em caso de falhas.
Facilidade e Eficiência na Diagnóstico de Problemas
Com um histórico de manutenção bem documentado, torna-se mais fácil diagnosticar problemas quando surgem. Os técnicos que realizam as manutenções podem se referir a registros anteriores para identificar padrões e causas de falhas, facilitando a solução de problemas. Isso não apenas economiza tempo, mas também garante que as soluções aplicadas sejam mais precisas e eficazes, resultando em reparos mais rápidos e eficientes.
Valorização do Equipamento
Por fim, a manutenção regular valoriza o grupo gerador quando chega a hora de revender ou substituir o equipamento. Um gerador bem mantido geralmente tem maior valor de mercado, pois os potenciais compradores perceberão o cuidado e a atenção que foram dados ao equipamento ao longo do tempo. Isso pode resultar em um retorno financeiro significativo quando é hora de fazer um upgrade ou trocar o gerador por um modelo mais novo.
Em resumo, os benefícios da manutenção regular de grupos geradores são incalculáveis e fundamentais para garantir um ambiente operacional eficiente e seguro. A prática de manter o gerador em boas condições não apenas prolonga sua vida útil, mas também traz economia, confiabilidade e segurança ao processo de geração de energia. Investir em manutenção regular deve ser uma prioridade para todos que utilizam grupos geradores, assegurando não apenas a eficiência do equipamento, mas também a proteção do investimento realizado.
Como Realizar um Check-up Eficiente
Realizar um check-up eficiente em grupos geradores é uma prática essencial para garantir o funcionamento adequado e a longevidade do equipamento. Essa atividade envolve a inspeção e a manutenção de diversos componentes, assegurando que não haja falhas que possam comprometer o desempenho do gerador. Neste artigo, abordaremos as principais etapas e práticas necessárias para realizar um check-up eficiente, promovendo a segurança e a eficácia do seu sistema de energia.
Planejamento e Frequência do Check-up
Antes de iniciar um check-up, é fundamental planejar a atividade com base na frequência recomendada para manutenção. As manutenções devem ser programadas de acordo com as orientações do fabricante e a intensidade de uso do gerador. Além disso, mantenha um registro detalhado dos check-ups realizados, incluindo as datas e as atividades executadas. Isso não apenas ajuda a acompanhar o histórico de manutenção do gerador, mas também facilita o planejamento de futuras intervenções.
Ferramentas e Equipamentos Necessários
Para realizar um check-up eficiente, é necessário ter à disposição as ferramentas e os equipamentos adequados. Isso pode incluir chaves de roda, multímetros, manômetros, ferramentas de ajuste, lubrificantes e produtos de limpeza. Além disso, é importante utilizar equipamentos de proteção individual (EPIs), como luvas e óculos de segurança, para garantir a segurança do operador durante o processo. A preparação antecipada garante que todas as ferramentas necessárias estejam à mão, evitando interrupções durante o check-up.
Inspeção Visual Inicial
O check-up deve começar com uma inspeção visual do gerador. Verifique se há sinais de danos, corrosão ou desgaste visíveis, como vazamentos de óleo, contaminação do combustível ou rachaduras nas partes externas. A inspeção visual é uma etapa crucial que pode revelar problemas antes que eles se tornem críticos. Fique atento a qualquer alteração na aparência do equipamento que possa indicar a necessidade de reparos.
Verificação dos Níveis de Óleo e Combustível
Certifique-se de verificar os níveis de óleo e combustível do gerador. Um nível baixo de óleo pode causar danos permanentes ao motor, enquanto um nível inadequado de combustível pode impedir que o gerador funcione corretamente. Adicionalmente, verifique a qualidade do óleo, pois o óleo sujo ou queimado deve ser trocado. A troca regular de óleo e o monitoramento dos níveis são práticas essenciais para manter o motor em boas condições.
Inspeção do Sistema de Arrefecimento
O sistema de arrefecimento é fundamental para o funcionamento adequado do motor, evitando superaquecimentos. Durante o check-up, verifique o nível e a condição do líquido de arrefecimento. O radiador e as mangueiras também devem ser inspecionados quanto a vazamentos e obstruções. Manter o sistema de arrefecimento em boas condições é vital para a segurança do gerador e para a prevenção de falhas graves.
Verificação do Sistema Elétrico
Inspecione o sistema elétrico, incluindo conectores, fiação e bateria. Verifique as conexões para garantir que estejam firmes e livres de corrosão. Um teste da bateria deve ser realizado para garantir que ela mantém a carga correta. Além disso, cheque os fusíveis e relés, pois componentes elétricos defeituosos podem causar falhas no sistema. A saúde do sistema elétrico é essencial para garantir que o gerador funcione corretamente quando necessário.
Testes de Operação
Um check-up eficiente deve incluir testes de operação para avaliar o desempenho do gerador. Inicie o gerador e observe seu funcionamento. Fique atento a ruídos anormais, flutuações de tensão e o tempo de resposta ao iniciar. Teste também o gerador sob carga, se possível. Isso ajudará a garantir que todos os componentes estão funcionando de acordo com as especificações do fabricante. Verificar a performance sob condições de carga é crucial para antecipar possíveis problemas.
Limpeza e Organização
A limpeza é uma parte importante do check-up. Remova qualquer sujeira, detritos ou combustíveis acumulados ao redor do gerador. Isso não apenas melhora a aparência do equipamento, mas também ajuda a prevenir incêndios e outras situações perigosas. Uma área de trabalho limpa e organizada é essencial para a segurança operacional e contribui para a eficácia do check-up.
Documentação das Atividades Realizadas
Após concluir o check-up, é fundamental documentar todas as atividades realizadas. Mantenha um registro detalhado das inspeções, trocas de óleo, reparos e qualquer outra manutenção executada. Isso ajudará a manter um histórico de serviço do gerador e facilitará futuras manutenções. A documentação não apenas fornece referência valiosa, mas também pode ser crucial para reclamações de garantia ou contratos de manutenção.
Conclusão
Realizar um check-up eficiente em grupos geradores é uma etapa crítica para garantir o desempenho ideal e a segurança do equipamento. Com um planejamento adequado, a utilização das ferramentas certas e a verificação minuciosa de cada componente, é possível manter o gerador em ótimas condições de operação. Lembre-se sempre de seguir as recomendações do fabricante e de manter registros detalhados das manutenções. Isso não só garantirá um equipamento eficiente, mas também proporcionará tranquilidade ao saber que o gerador estará pronto para operar sempre que necessário.
Custos Associados à Manutenção de Grupos Geradores
A manutenção de grupos geradores é uma responsabilidade significativa para empresas e indivíduos que dependem desse equipamento para garantir a continuidade do fornecimento de energia. No entanto, é essencial entender que a manutenção pode envolver uma variedade de custos que vão além dos simples serviços de reparo. Neste artigo, discutiremos os diversos custos associados à manutenção de grupos geradores, ajudando proprietários e gestores a tomarem decisões informadas e econômicas.
Custos Diretos de Manutenção
Os custos diretos de manutenção incluem todos os gastos que envolvem a intervenção direta no grupo gerador. Isso abrange várias áreas, entre as quais:
- Serviços de Mão de Obra: O custo dos serviços prestados por técnicos especializados geralmente representa uma grande parte dos custos de manutenção. Profissionais qualificados podem cobrar tarifas horárias ou um valor fixo por serviço. É vital escolher prestadores de serviços com boa reputação para garantir que a manutenção seja feita corretamente.
- Peças de Reposição: Com o tempo, algumas partes do gerador podem se desgastar e precisar ser trocadas. Filtros, correias, bombas e outros componentes podem variar significativamente em preço. Ter um estoque de peças recomendadas pelo fabricante pode reduzir o impacto financeiro de falhas repentinas.
- Materiais e Lubrificantes: No processo de manutenção, frequentemente são necessários materiais, como óleo, graxa e produtos de limpeza. Esses insumos também devem ser considerados nos custos de manutenção, pois sua compra regular pode se acumular ao longo do tempo.
Custos Indiretos de Manutenção
Os custos indiretos de manutenção são aquelas despesas que podem não ser imediatamente evidentes, mas que têm um impacto significativo nas operações e receitas. Esses incluem:
- Tempo de Inatividade: Cada vez que um grupo gerador passa por manutenção, seja preventiva ou corretiva, pode haver períodos em que ele não está operacional. O tempo de inatividade pode resultar em perda de receita, especialmente se o gerador for fundamental para as operações da empresa. Avaliar o custo do tempo de não operação é necessário para entender totalmente os custos de manutenção.
- Impacto na Produção: Em ambientes industriais, uma falha no gerador pode interromper a produção. Isso pode resultar em perdas financeiras que vão além do custo direto da manutenção. A interrupção dos níveis de produtividade pode aumentar os custos operacionais e impactar a satisfação do cliente.
Custos Emergenciais
Quando a manutenção não é realizada de maneira eficiente e preventiva, podem surgir custos emergenciais, que são muitas vezes muito mais altos do que os custos de manutenção programada. Esses custos incluem:
- Reparos Urgentes: Quando ocorre uma falha inesperada, o custo dos reparos tende a ser mais elevado, já que a necessidade de soluções rápidas muitas vezes leva a um aumento nas tarifas cobradas por técnicos. Além disso, a urgência pode resultar na compra de peças a preços mais altos devido ao acesso imediato.
- Custos Adicionais: Custos relacionados a danos colaterais causados por quebras, como a necessidade de substituição de equipamentos danificados ou perda de bens, são consequências diretas de uma má gestão de manutenção, podendo gerar um gastos consideráveis.
Benefícios de um Programa de Manutenção Preventiva
Um programa eficaz de manutenção preventiva é uma forma de reduzir os custos gerais associados à manutenção dos grupos geradores. A manutenção preventiva ajuda a identificar problemas antes que eles se tornem falhas mais graves, resultando em:
- Menor Frequência de Manutenção Corretiva: Com revisões regulares, o número de reparos inesperados e custos emergenciais tende a diminuir, o que resulta em economia a longo prazo.
- Aumento da Eficiência: Grupos geradores que recebem manutenção adequada frequentemente apresentam desempenho melhorado, resultando em menores custos operacionais e consumo de combustível.
- Simplificação da Documentação Financeira: O acompanhamento de manutenções e seus custos ajuda a criar uma previsão mais precisa de gastos futuros, facilitando a gestão financeira.
Considerações Finais
Os custos associados à manutenção de grupos geradores variam amplamente, dependendo do tipo de equipamento, da maneira como é utilizado e da eficiência na gestão da manutenção. Portanto, é fundamental para proprietários e operadores de grupos geradores compreenderem completamente todos os custos envolvidos. Investir em manutenção preventiva e um bom planejamento é uma estratégia econômica que não apenas reduzirá os custos a curto prazo, mas também prolongará a vida útil do equipamento e melhorará sua eficiência geral.
Além disso, sempre que possível, procure consultoria especializada e avalie contratos de manutenção que ofereçam suporte contínuo. Esta abordagem garantirá não apenas a otimização dos custos, mas também a segurança e a confiabilidade do seu sistema de geração de energia.
Em conclusão, a manutenção preventiva e corretiva de grupos geradores é crucial para assegurar que esses equipamentos operem de maneira eficiente e segura. Ao compreender a importância de cada uma dessas práticas, assim como as diferenças entre elas, os proprietários e operadores podem tomar medidas proativas para garantir a longevidade e o desempenho de seus geradores. Inspecionar regularmente os principais componentes, seguir uma frequência recomendada de manutenção e estar atento aos sinais que indicam a necessidade de intervenção corretiva são passos indispensáveis para otimizar a performance do seu grupo gerador. Com um planejamento adequado e uma abordagem sistemática, é possível não apenas evitar falhas inesperadas, mas também maximizar o retorno sobre o investimento nesse equipamento essencial. Portanto, mantenha sempre a manutenção em dia e leve a sério a saúde do seu sistema de geração de energia.
Gostou? compartilhe!
Gostou? compartilhe!